تیغه های اره الماسی عمدتاً برای برش مصالح سنگی سخت و شکننده استفاده می شود و یکی از ابزارهای اصلی برای تولید اسلب سنگ طبیعی است. تیغه اره الماسی با جوش دادن قطعات الماس بر روی یک بستر مدور ساخته می شود.
برای اطمینان از عملکرد مناسب برش، بستر تیغه اره الماسی باید الزامات خاصی را برآورده کند. باید استحکام و استحکام کافی داشته باشد بدون اینکه بیش از حد نرم باشد. این در نیاز به سختی کافی منعکس می شود. یکی دیگر از ویژگی های مهم زیرلایه، توانایی آن در مقاومت در برابر لرزش های شدید در هنگام استفاده است. از آنجایی که قطعات ضخیم تر از بستر هستند، یک شکاف بین زیرلایه و سنگ در حال برش در حین کار وجود دارد. برای جلوگیری از افت زودرس استحکام یا ترک خوردگی ناشی از ارتعاش، بستر باید دارای سطح خاصی از شکلپذیری، حد خستگی بالا و حد الاستیک باشد تا ضربهها را کاهش داده و ارتعاشات را به طور موثر جذب کند.
بر اساس استانداردهای فنی برای زیرلایههای تیغه اره الماس، دستیابی به حد الاستیک و سختی مورد نیاز شامل یک فرآیند عملیات حرارتی خاموش کردن و به دنبال آن گرم شدن در دمای متوسط است. برای تیغه های اره الماس ساخته شده از فولاد 65Mn به عنوان ماده زیرلایه، این فرآیند به ویژه مناسب است. با این حال، یک چالش مهم در فرآیند کوئنچ، تمایل زیاد برای تغییر شکل و ترک است.
علل تغییر شکل
1. گرمایش: در حین گرم کردن، چه در حمام هوا یا نمک، همرفت حرارتی درجه خاصی از تأثیر را بر بستر وارد می کند و به طور بالقوه باعث تغییر شکل گرمایش می شود.
2. خنکسازی: نرخهای خنککننده ناهموار در بخشهای مختلف بستر منجر به اختلاف دما میشود که منجر به انقباض حرارتی ناهموار فولاد و ایجاد تنش حرارتی میشود. علاوه بر این، در طول کوئنچ، تبدیل از آستنیت فوق سرد به مارتنزیت شامل تغییرات در حجم خاص است که باعث تنش ساختاری و تغییر شکل تبدیل فاز می شود.
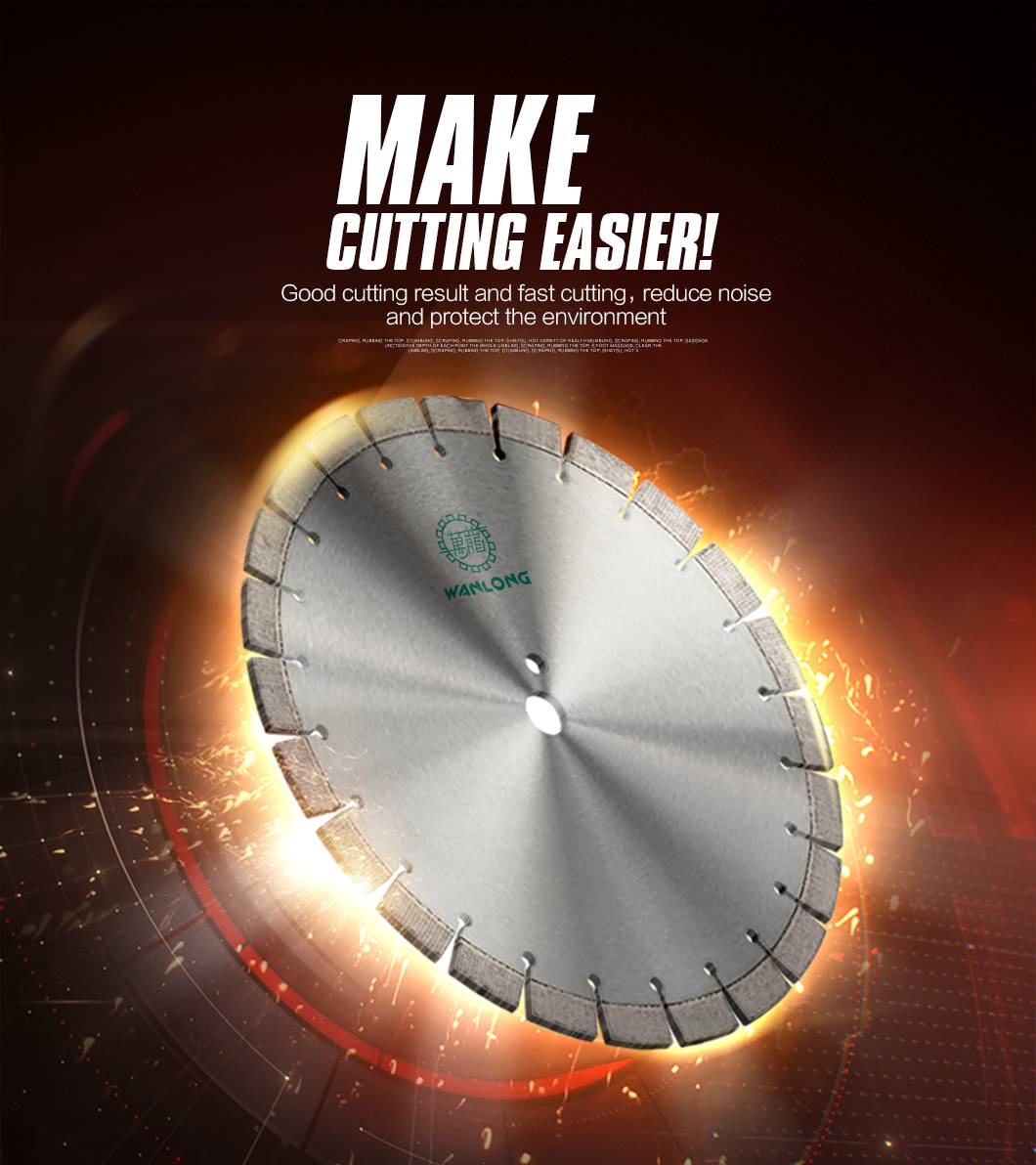
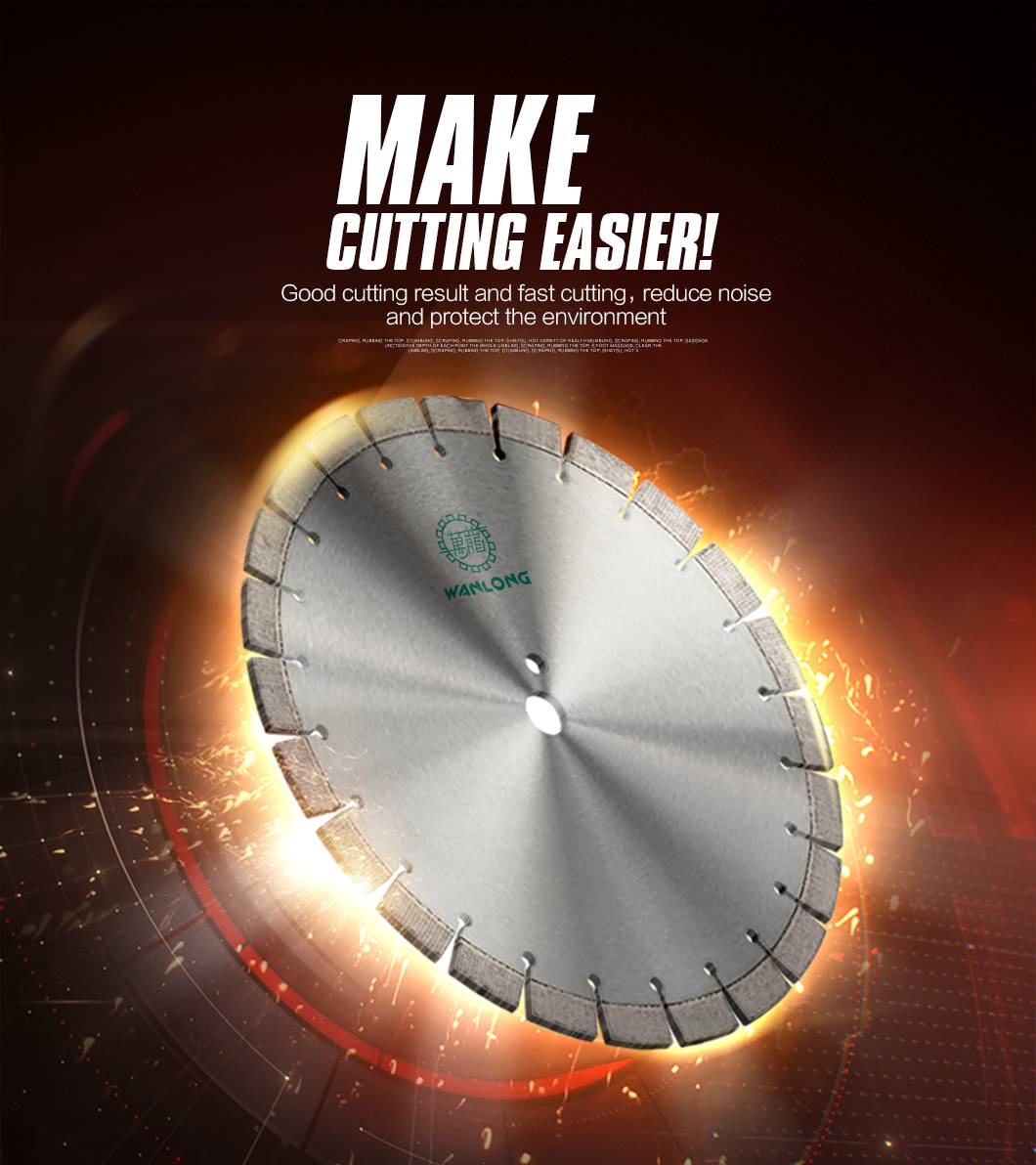
عوامل موثر در ایجاد ترک
عوامل متعددی می توانند در ایجاد ترک نقش داشته باشند، از جمله:
- ترکیب شیمیایی فولاد.
- نقص در مواد اولیه.
- ساختار اصلی مواد.
- عوامل گرمایشی
- عوامل خنک کننده
- ویژگی های ساختاری منحصر به فرد تیغه های اره، مانند تمرکز تنش در لبه های تیغه، به ویژه افزایش تنش کششی در حاشیه، که پتانسیل تشکیل ترک را افزایش می دهد.
اهمیت عملیات حرارتی
خواص مکانیکی زیرلایه تیغه اره الماس به طور قابل توجهی بر کیفیت و عملکرد آن تأثیر می گذارد. در این میان، فرآیند عملیات حرارتی نقش مهمی در تعیین خواص مکانیکی دارد. کنترل مناسب این فرآیند تضمین می کند که زیرلایه به تعادل مطلوب سختی، شکل پذیری و مقاومت در برابر تغییر شکل و ترک دست می یابد و در نتیجه عملکرد و دوام کلی تیغه را افزایش می دهد.