Bei der ersten Inbetriebnahme der Brückenschneidemaschine stellen Anfänger häufig fest, dass der Schnittbereich des Werkstücks nicht ideal und die Ebenheit nicht gut ist, was zu minderwertiger Genauigkeit oder sogar zu Ausschuss führt, was sehr ärgerlich ist. Was genau verursacht dieses Problem und warum wurde es nicht vollständig gelöst?
1. Ein Punkt, den Benutzer von Schneidemaschinen oft übersehen, ist die Instabilität des Schneidetisches, der die Stahlplatte trägt. Aus diesem Grund verlangen wir von unseren Kunden immer, dass sie Schneidetische gemäß den Standards herstellen. Wenn der Schneidetisch unsachgemäß verwendet wird oder nicht fest verschweißt ist oder wenn schwere Maschinen in der Nähe Vibrationen verursachen, schwingt oder verschiebt sich die Stahlplatte während des Schneidevorgangs und die Ebenheit der Schneidefläche nimmt ab.
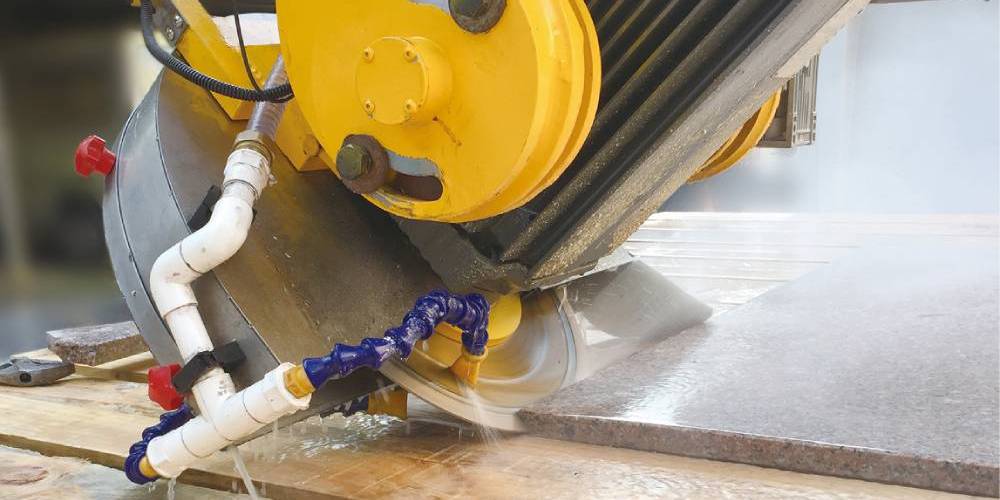
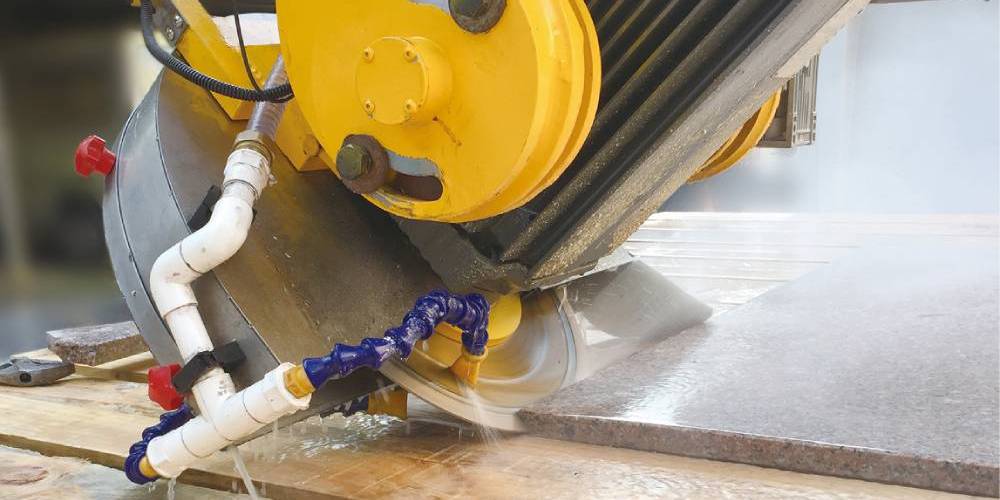
2. Der Spalt an der Verbindung des mechanischen Teils ist zu groß. Beispielsweise besteht ein Spalt zwischen Motor und Getriebe, die Halterung des Schneidbrenners ist nicht fest angebracht, die Vorrichtung zum Anheben und Verstellen der Höhe des Schneidbrenners ist instabil, das Lauflager der horizontalen Hängeplatte ist nicht konzentrisch oder beschädigt usw. Die oben genannten Situationen führen dazu, dass der Schneidbrenner während der Bewegung wackelt, was zu zahnähnlichen Wellen auf der Schneidfläche führt.
3. Die Vertikalität des Schneidbrenners im Verhältnis zur Stahlplatte beeinflusst auch die Schneidwirkung. Daher ist es auch sehr wichtig, die Vertikalität des Schneidbrenners vor dem Schneiden zu kalibrieren.