1. Diamond grinding wheels mainly use the profiling method without considering abrasives, pores and fillers. After weighing the abrasive and bonding agent according to the weight ratio of the formula, put them into a mixer to mix evenly and then put them into a metal mold. The grinding tool blank is formed on a press.
2. After drying the grinding wheel blank, put it into the kiln for baking. The firing temperature is generally around 1300℃.
3. When using low melting point sintering binder, the firing temperature should be lower than 1000℃.
4. Then process it according to the specified size and shape, and then inspect the product to strictly control the quality.
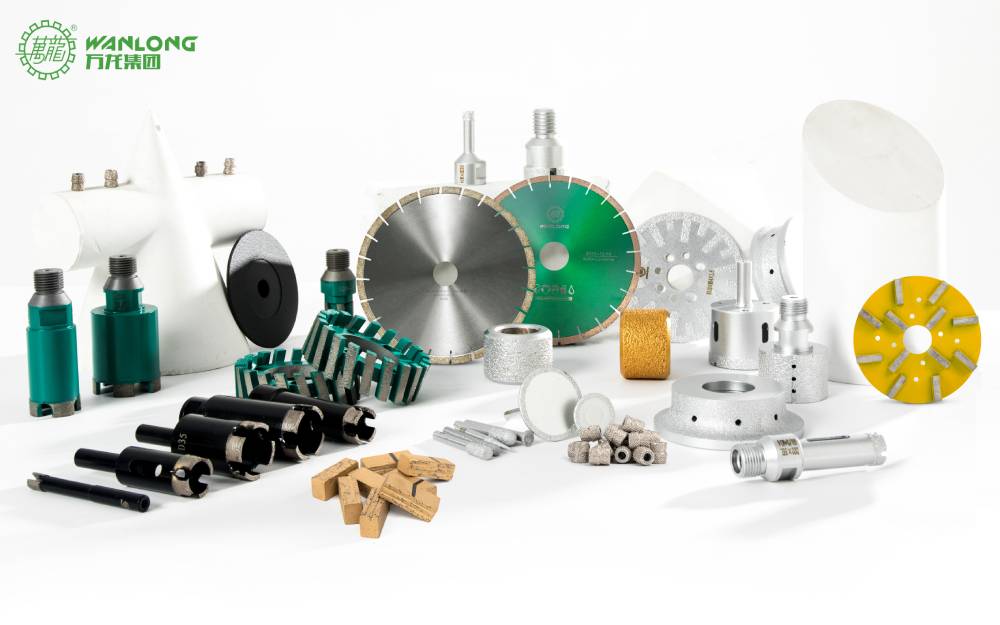
Diamond grinding wheels use diamond abrasives as raw materials, and metal powder, resin powder, ceramics and electroplated metal as binding agents. The circular bonded abrasive tool with a through hole in the middle is called a diamond grinding wheel (alloy grinding wheel).
Diamond grinding wheels have the advantages of high hardness, good wear resistance, and strong compressive strength. They are ideal grinding tools for grinding hard materials and carbide.