For example, if we choose too high a diamond density or too good a diamond, its sawing performance will not be very good. Diamonds are less likely to break, making it difficult to form new sharp edges.
2. When the saw wire breaks, it is usually caused by using the wrong application parameters or the quality of the diamond bead wire saw is too poor, which means that the bond between the plastic/rubber and the diamond beads is not strong, causing chips to enter the diamond saw wire, This is very likely to happen. Soon, the magma or rock debris part between the beaded steel body and the wire rope comes into contact and rubs against the wire rope, and the connecting wires of the wire rope begin to break. This can also be caused by improper application of adhesive.
Incorrect selection of the steel wire rope and beaded steel body, and poor heat treatment after injection molding may also cause the wire rope to break.
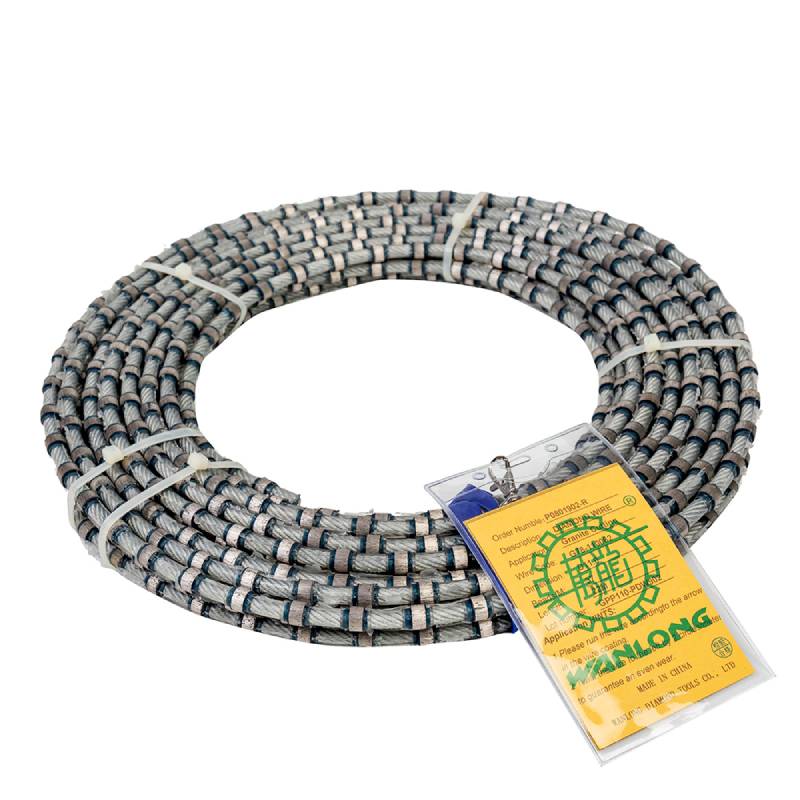
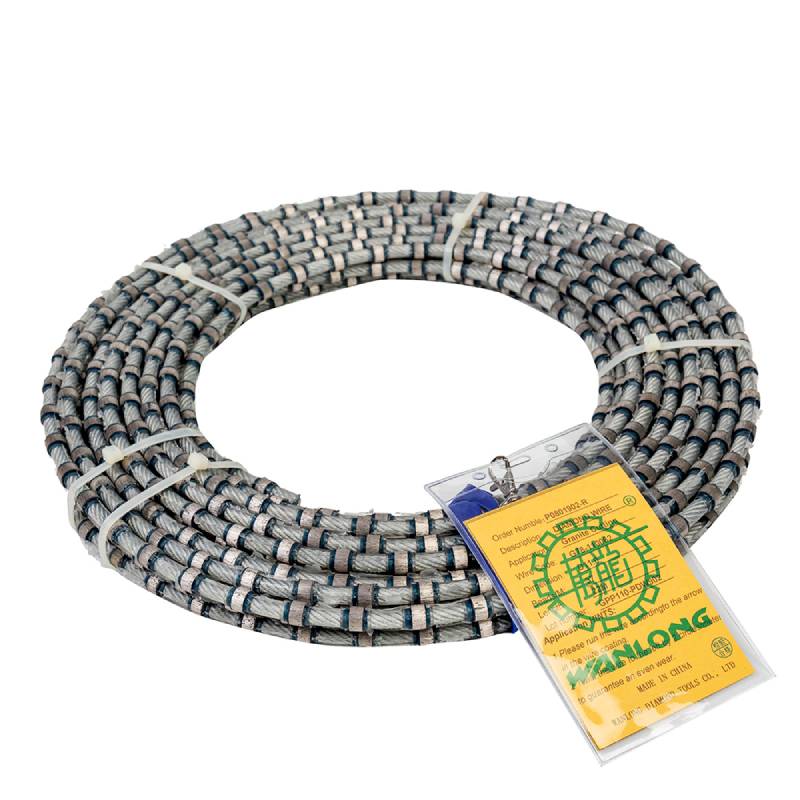
3. Bead peeling off: If the bead cutting layer peels off from the beaded steel body, it is usually caused by improper selection of the matrix or the use of wrong sintering parameters. Often using an incorrect cold pressing process is also a cause of spalling.
Sometimes, due to improper dewaxing process, paraffin may penetrate between the metal carcass and the beaded steel body. Sometimes the problem is also related to improper cleaning of the beaded steel body.
4. The beads are not firmly bonded. Loose beads and weak bonds are often signs of problems during the injection molding process. It may also be related to improper selection of steel wire rope, or improper internal contamination and cleaning of diamond beads, which will lead to weak bonding force between beads and injection molding/injection rubber.