Suppose that when the diamond wire saw starts to calculate, a bead on the wire saw has just completely entered the arc area; the texture of the processed stone is uniform.
Regardless of the role of the coolant, the beads are uniform heat-conducting media; the frictional influence of the chips is ignored; all the energy consumed during the machining process is converted into heat energy, and all the heat is transferred to the tool; the boundary condition is an adiabatic boundary; each small bead is An independent heat source etc.
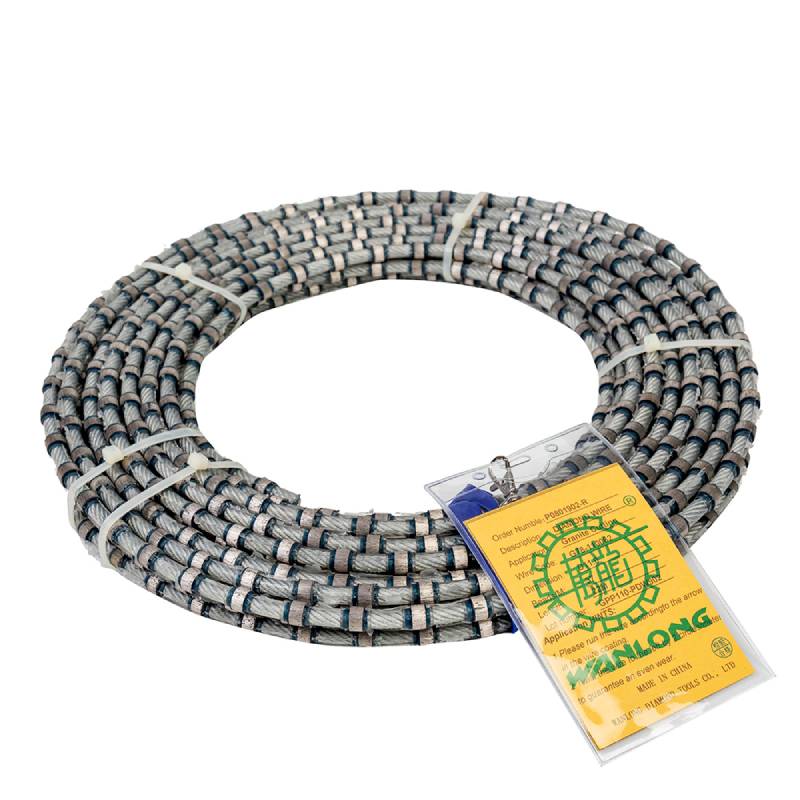
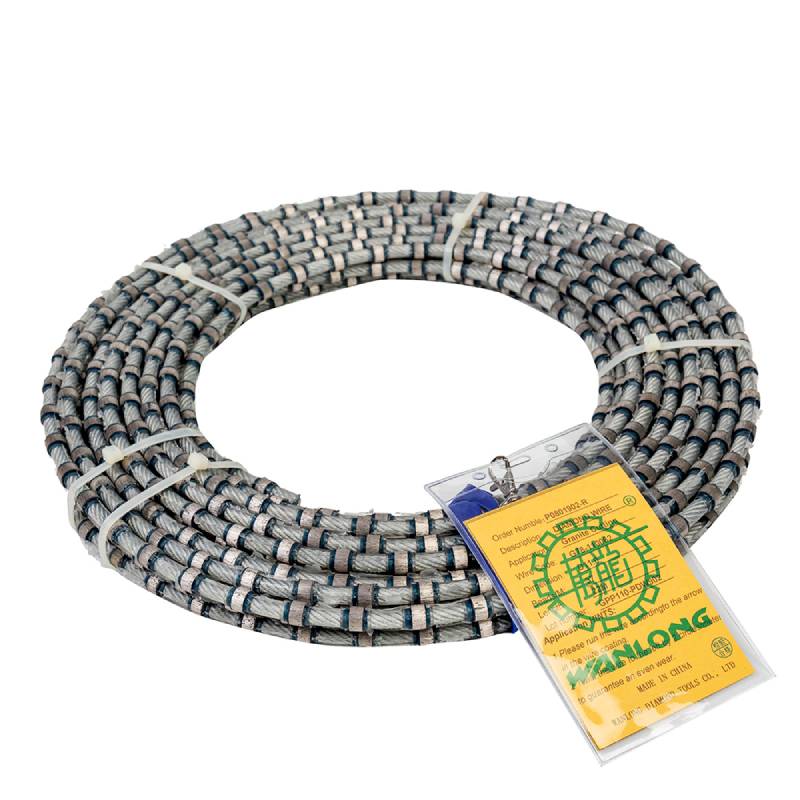
Unlike a large number of studies on heat source models in metal cutting and grinding processes, there is a relative lack of research on theoretical analysis models of temperature fields suitable for wire saw processing.
The current theoretical model of diamond wire saw processing temperature field is established based on the research results of the temperature analysis model of large depth of cut intermittent grinding.