(1) Automatic line grinding and polishing machine The automatic line grinding and polishing machine is an equipment that has been developed in the past two years to achieve mechanized grinding and polishing of lines. It can realize line shaping, grinding and polishing, side grinding and polishing of lines, and assembly line production, thereby improving line production efficiency and product quality, improving the working environment of employees, and reducing labor intensity. This is a breakthrough and innovative technology in the field of stone deep processing, which has been gradually promoted and applied in the domestic stone industry. The automatic line machine breaks through the limitation that the previous automatic line grinding and polishing machine can only polish and polish natural stone materials. It can polish and polish artificial granite materials, which takes the technology forward a big step. At present, many domestic stone production enterprises have purchased a fully automatic liner, which has its unique technical advantages and innovation:
1. All the processes of forming, side thickness setting, polishing, and side polishing complete the line, and directly produce the finished product. 2. The combined circular saw blade rough machining + forming wheel fine milling modeling mode has successfully solved the disadvantages of similar equipment such as low forming efficiency, high production cost, and rough forming surface, making the formed lines more delicate and precise. The combined diamond saw blade not only inherits the advantages of traditional diamond saw blades with high modeling efficiency, but also exerts the advantages of the overall shape of the forming knife. Combining the technical advantages of the two, improves the efficiency of line forming. The combination of saw blades of different diameters is used to form lines of different shapes, and the processed parts are rough processed. Combination saw blade shape diagram
3. The equipment only needs one thick (60#) and one thin (120#) forming milling wheel to complete the finishing milling of the line, which reduces 2 milling wheels compared with the same period last year, which can achieve the purpose of reducing production costs. 4. Low breakage rate. Because the saw blade is used for forming, the contact surface is small and the cutting is sharp, so the pressure on the stone and the forming wheel to the line is reduced. In particular, it has a great protective effect on product materials that are easy to break and small lines, reducing the rate of product damage and improving the economic benefits of enterprises.
5. Low conversion cost, suitable for small batch line production. The circular saw blades with different shapes and diameters are combined to form various lines and curves. When the shape of the processed line changes, you only need to re-adjust the saw blade sequence and combine the saw blades to achieve the purpose of changing the line shape.
6. The operation is flexible and convenient, without the need for professional operators. The use of advanced programmable control technology overcomes the shortcomings of similar equipment such as simple control system, fixed lifting speed of the forming polishing wheel, and constant pressure, making the operation simpler and more convenient, and the product quality more stable. The polishing system and lifting system of the automatic line grinding and polishing machine adopts an advanced numerical control system, which controls the lifting of the polishing head by driving a high-precision stepping motor. This kind of CNC lifting system can set different polishing grinding head speed and polishing grinding head lifting speed according to the structure, thickness, density, gloss of the stone and different abrasive sharpness. With the cooperation of linear guide rail and precision screw, it is precise Drop to the workpiece on the polished surface, and continue to polish the workpiece according to the set pressure.
Each group of motors of the automatic line grinding and polishing machine is equipped with a speed sensor, which can detect the pressure and changes on the surface of the polished workpiece at any time, and can feedback to the polishing grinding head CNC lifting system at any time according to the pressure change. The numerical control system adjusts the descending speed of the polishing head in time, so that the rotation speed of the polishing head is always in the optimal range, greatly reducing the consumption and waste of the polishing head, and making the surface polishing of the line more delicate and higher. 7. There is an intelligent operating system that can realize man-machine dialogue. The system consists of a programmable controller and a touch screen. According to the shape, material, density and hardness of the stone line to be processed, the working procedure of each group of polishing grinding head can be formulated in accordance with the density and mesh number of the polishing grinding head. When the polishing head is working, once the surface pressure of the polished workpiece changes, it can automatically adjust the rotation speed and descending speed of the polishing head, so that the polishing head is always in the best working state during polishing. 8. Stable transmission system. The entire assembly line has a set of stable and high-precision conveying devices, which can ensure that the lines to be polished accurately and continuously enter the polishing work area, so that the polishing head can accurately polish and polish the lines. 9. Tamron edging machine. Tenglong edging machine is a small stone processing machine manufactured by Jiangsu Suzhou Nanhang Tenglong Technology Co., Ltd. It is suitable for edging and small-line processing modeling and polishing of stone products. It is a small area and cheap stone processing equipment. The Tamron edging machine is composed of four parts: worktable (D), frame (A), head (B) and control box (C).
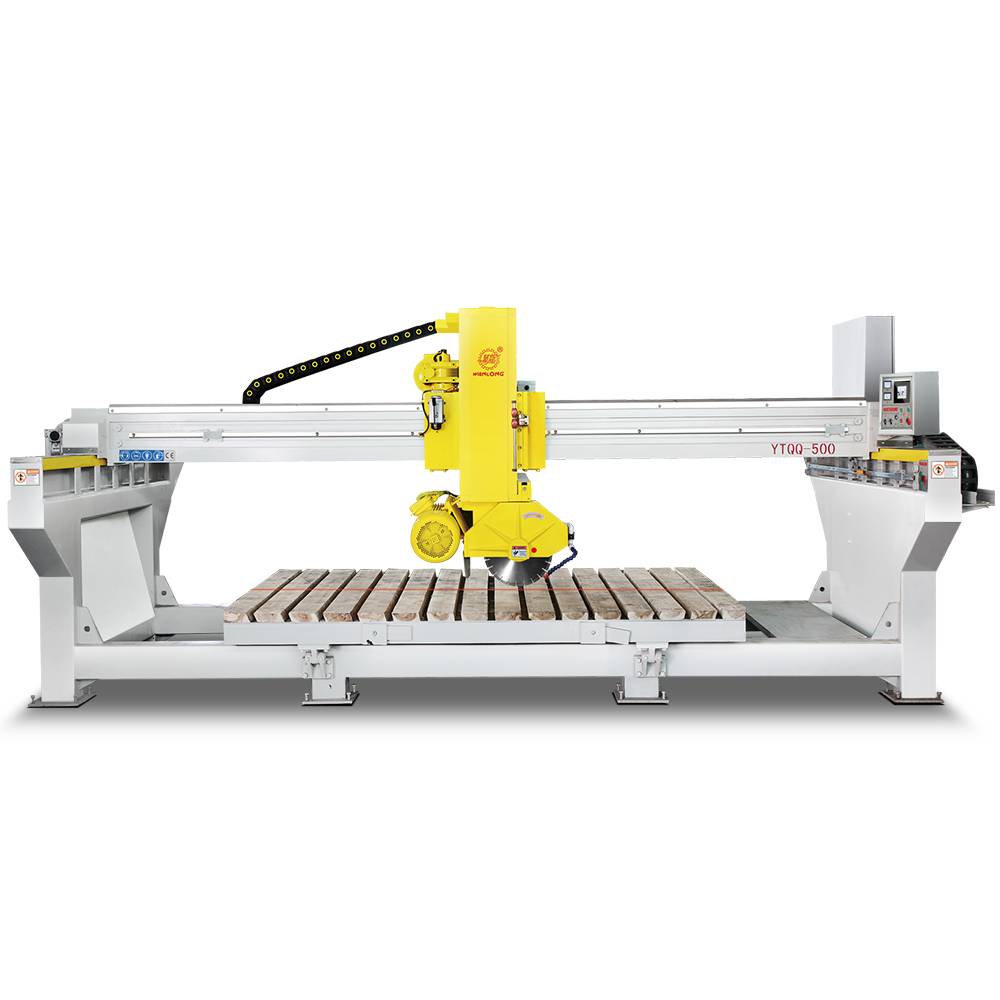
The handwheel 2 on the frame A controls the machine head B to move left and right in the horizontal direction. There is a scale ruler on the horizontal rail, which can read the distance moved in the horizontal direction more accurately. The handwheel 1 on the frame A controls the machine head B to move up and down in the vertical direction. There is a scale ruler on the vertical rail, which can accurately read the distance of the machine head moving up and down. The movement of the machine head up, down, left and right plays a very important role in actual processing. Tamron edging machine Quick tool change device: The tool holder of the grinding wheel in the figure below is a quick tool change device. It can be used in conjunction with the special wrench of the Tamron edging machine to quickly replace the grinding and polishing wheel during the grinding and polishing process, thereby improving the production efficiency of the grinding and polishing operation. Higher, reducing tool change time. Workpiece clamping quick fixture: a device for rapid clamping of workpieces, which can save the time of workpiece clamping. Quick tool change Quick splint 2. Matte and smooth surface processing equipment for arc board (1) Automatic line grinding and polishing machine The automatic arc plate automatic grinding and polishing machine is a special equipment for water grinding and polishing of stone arc plates. There are three models of single-head, double-head and three-head. Its characteristics are as follows: 1. It is mainly suitable for the automatic grinding and polishing of stone arc slabs and solid columns of 3 or more pieces.
2. The biggest feature of the three-station automatic arc plate polishing machine is that it has A, B and C three grinding heads, three workbenches are independent of each other, and three arc plates are polished at the same time, which realizes the increase of single machine, single person and single shift output. 3. The equipment is equipped with a pneumatic system to adjust the lifting pressure of the grinding head to adapt to the processing of different stones to achieve the purpose of improving the brightness of the product. 4. The left and right walking speed of the grinding head and the turning speed of the worktable are passed through the frequency converter, and the control speed is steplessly adjustable to adapt to the processing of arc plates with different widths. 5. The workbench is equipped with special fixtures, the arc plate is positioned, clamping and disassembling are particularly convenient. Compared with the traditional manual or vertical lathe cylindrical processing method, it has great advantages and makes the processing simple and easy.
6. The electrical system is controlled by PLC, and the operation panel is equipped with a liquid crystal display, which is convenient for intuitive operation and reliable operation. The automatic arc plate polishing machine should be used in conjunction with the arc plate rough grinding machine. First, use the arc plate roughing machine to roughen the arc plate processed by the CNC arc plate wire saw to eliminate the processing traces and processing errors of the arc surface, and make the radius and arc of the arc surface more accurate. After the rough grinding is finished, it is then polished with an automatic arc plate polishing machine. The brightness of the arc plate polished by this process can be exactly the same as that of the large plate of the same material. The arc rough grinder is only suitable for R in the range of 350 to 1050mm. When R is out of this range, other equipment should be considered for polishing. Such as NC grinding, three-head hand-grinding arc plate polishing machine.
Arc plate rough grinding machine Double-head automatic arc plate polishing machine (2) Fully automatic single-arm arc plate polishing machine The automatic single-arm arc plate polishing machine is more efficient than the double-head automatic arc polishing machine. It can grind and polish 3 arc plates at the same time; the range of polishing and polishing arc plates is wider, not only can grind and polish small radii The arc plate can also be polished and polished with a large radius. After it is modified, the solid column can also be polished. When this kind of machine is grinding and polishing the arc plate, the worktable can either make a circular swing movement, or it can make a horizontal movement along the horizontal guide rail. Automatic single-arm cylindrical polishing machine 3. Grinding and polishing equipment for cylindrical matte surface and smooth surface Numerical control lathe: Full computer control has a high degree of automation. Only one program is needed to make the equipment complete the work of polishing and matting solid columns, and the polished solid columns have high luminosity, and the luminosity of the solid columns can be polished into glass luster. , The luminosity reaches above 100°. The equipment is produced in Italy, and only a few stone manufacturers in China own it. Horizontal and vertical lathes: It can be used for cylindrical modeling, as well as matte and smooth surface. Vertical lathe CNC lathe Horizontal lathe Four, side matte, smooth surface polishing equipment Fully automatic continuous edging machine is equipment for polishing and matting the edging of plates. The largest production volume in the processing of stone products is none other than the edging products in the engineering board. See polished edge, hypotenuse, chess piece edge, 1/4 arc edge, polished edge + bottom, chicken mouth, hypotenuse + polished edge. At present, the processing of these products is basically done by manual polishing in many stone factories. The processing quality is low. The polished edges vary from person to person, the size is inconsistent, the randomness is large, the production efficiency is low, and the products are not interchangeable after processing. In the production process, there is a lot of dust and pollute the environment. The above drawbacks can be solved by using a fully automatic continuous edging machine. This full-automatic continuous edging machine is processed with the smooth surface positioned facing down, and the processing quality is not limited by the thickness of the plate, and the processed products are consistent with good interchangeability.
The OMEGA100 automatic continuous edging machine in the picture integrates the processing functions of multiple machines to complete a series of processes such as forming, top chamfering, bottom chamfering, and grinding and polishing of a plate. At the front end of the machine, saw blades and forming wheels can be installed to complete the processing of chicken mouth, slotting, inverted beveling, and forming. 8 grinding heads are installed on the machine to complete the beveled edge, the bright edge, and the R-shaped chess edge. 1/4 round edge grinding and polishing work. The edging angle of this machine is 0°~180°, the minimum width of the edging board is 250mm, and the maximum width is 1500mm. If the conveying part of the equipment is appropriately improved, the processing width can be wider. Automatic continuous edging machine 5. Mirror surface processing equipment and tools Mirror surface processing equipment and tools mainly include: floor grinder, floor scrubbing machine, water suction machine, multifunctional floor scrubber, blow dryer, dryer, scouring pad, polishing pad, bucket, mop, small trowel, rag . The ground grinder, also known as the stone crystal surface machine, is an electric device for polishing and polishing the ground stone and processing the crystal surface. Generally, the rotation speed is about 220 rpm, and the weight of about 60KG is the most suitable, so that the stone can achieve the ideal crystallization effect. The stone crystal surface machine uses crystal surface treatment agent to repeatedly rub the stone surface. Under the dual action of chemical and physical, a hard and dense crystal hard crystal layer is formed on the surface of the ground, so that the stone surface is not easy to be damaged or stained, thus ensuring The essential characteristics of stone. Ground mill 6. Resin surface processing equipment, tools and materials (1) Resin surface processing equipment The resin surface processing equipment mainly includes: cutting, cutting, modeling equipment, edging equipment and grinding and polishing equipment. The grinding and polishing are mainly manual grinding and polishing. Cutting equipment: circular saw, single blade saw. Cutting equipment: bridge cutting machine, electronic bridge cutting machine, water jet machine.
Modeling equipment: automatic line machine, copying machine, computer bead wire saw, horizontal and vertical lathe, CNC lathe, edge grinding machine, engraving machine. Grinding and polishing equipment: automatic continuous polishing machine, automatic line grinding and polishing machine, vertical and horizontal lathes, single-arm hand grinder, automatic arc plate rough grinder and polishing machine. (2) Main materials for resin surface processing Yabang brand 6688 is an ortho-phthalic general unsaturated polyester resin with medium viscosity and medium reactivity, high product strength, good rigidity, good surface dryness, strong adhesion, high hardness and high transparency. It is suitable for the surface coating of high-grade natural stone, artificial marble and wood. Solvent-free epoxy varnish gold oil curing agent, solvent-free epoxy varnish gold oil main agent, leveling agent, defoamer, anti-oil agent, ring chlorine powder filling hole. The role of solvent-free epoxy varnishing oil: the role of improving gloss. A coating that can increase gloss and protect the inner layer when applied to the surface of the article. A resin with good film-forming properties is dissolved in a solvent (medium) to make a transparent and bright material with a certain fluidity and viscosity, which can improve the aesthetic level and other properties of the product. Overcoat varnish is generally a varnish without pigment, and the system generally has two types: UV and PU. (3) Resin surface tools and auxiliary materials The tools and auxiliary materials for the resin surface mainly include: scraper, sandpaper, electric angle grinder, electric water grinder, steam engine, hand-held polishing machine, polishing wool felt, measuring cup, and water scoop. The squeegee is mainly used to squeegee the surface of the processed product evenly. Sandpaper is used to polish and polish the resin surface. There are 60#, 80#, 120#, 220#, 320#, 400#, 500#, 600#, 800#, 1000#, 1500#, 3000#. Among them, 60#, 80#, 120#, 220# are mainly used for rough grinding; 320#, 400#, 500#, 600#, 800# are mainly used for fine grinding. The traces on the stone surface are further processed to produce Matte effect; 1000#, 1500#, 3000# are mainly used for polishing, which can produce true light effect. Electric angle grinder: It is mainly used to polish the parts of the product surface that are difficult to be roughed by hand to make the polishing quality better. Grinding machine: Electric water mill and steam engine are used for polishing products. Hand-held polishing machine: It is used to further polish the products that have been polished, so that the surface of the product has a higher gloss. Polishing wool felt: It is installed on the hand-held polishing machine and acts as an auxiliary material for polishing the product surface. Measuring cup: an auxiliary tool for measuring glue and curing agent. The measuring cup glue and curing agent should be used separately. Water scoop: used as an auxiliary tool when mixing glue. Seven, mechanical processing surface processing equipment, tools (1) Machining surface processing equipment Machining surface processing equipment mainly includes: cutting equipment, cutting equipment, and modeling equipment. Cutting equipment: circular saw, single blade saw, computer beaded wire saw. Cutting equipment: bridge cutting machine, electronic bridge cutting machine, water jet machine. Modeling equipment: automatic line machines, copying machines, computer bead wire saws, horizontal and vertical lathes, CNC lathes, edge grinding machines, engraving machines, CNC machining centers. Because the surfaces processed by these types of processing equipment are delicate, the patterns processed are complex, and the number of degrees is high, the most commonly used equipment for machining surfaces in these processing equipment is CNC machining centers, CNC lathes, and engraving machines. The CNC machining center is the most advanced stone processing equipment, used for processing complex three-dimensional geometric products, and the processing surface is smooth, high precision, suitable for mechanical surface processing of stone products. The product type processed by the computer beaded wire saw is a geometric body with straight lines, which is especially suitable for processing chairs, letters, and large curved surface lines. Because the beaded rope is a flexible tool, the processed surface has a water ripple mark, which is not suitable for processing mechanical surfaces. The mechanical surface processed by water jet machining is mainly the side surface of the product