Mining cutting machines are a good helper for stone manufacturers in mining. The mining cutting machine can work continuously for 8 hours a day and can produce a large amount of stone blocks, which can help stone manufacturers make a lot of money. Moreover, the maintenance rate of mining cutting machines is also very small, which will not cause great losses to the manufacturers. Having said that, if the mining cutter is not properly maintained, the mining cutter will retire prematurely. So how should we maintain the mining cutting machine?
1. A good foundation enables the mining cutting machine to work stably in the mine. Therefore, before installing the mining cutting machine, the foundation must be poured first, and the foundation maintenance period shall not be less than 20 days. The embedded anchor bolts, foundation size, location, etc. should comply with the drawing requirements.
2. Before using the mining cutting machine, all components must be inspected first. After the installation is completed, start the trial operation to observe the situation, and adjust the guide rail gap by inlaying the top screw to ensure smooth and flexible lifting without jamming or abnormal noise.
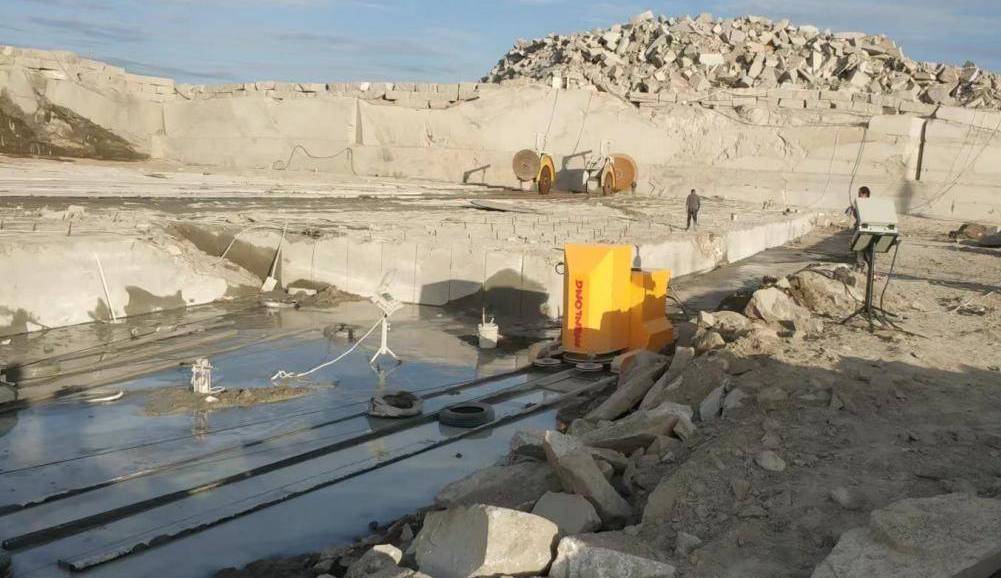
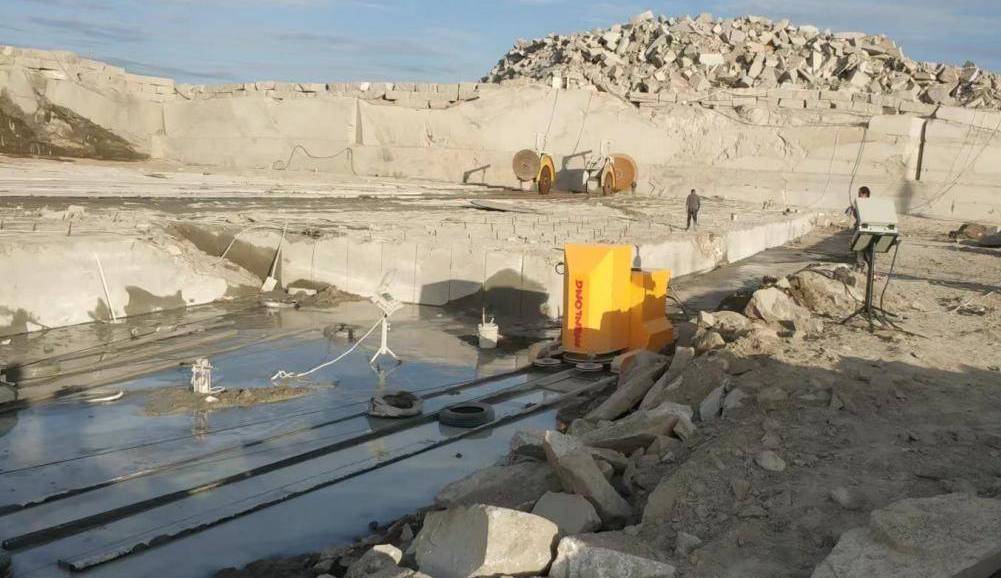
3. After the machine has been used for a period of time, the lubricating oil added previously will no longer work, so we must frequently check the lubrication of the machine. Once there is a need to add lubricating oil, the lubrication requirements must be strictly followed as soon as possible. Fill and change oil.
4. When replacing the diamond saw blade, the end face runout of the saw blade should be detected. New saw blades should not exceed 0.8mm, and re-welded saw blades should not exceed 1.5mm.
5. Install the spindle box on the carriage under the inner frame, and adjust the transmission position to ensure that the spindle rotates flexibly. The perpendicularity between the spindle and the crossbeam should not be greater than 0.06mm, and the runout of the flange end face of the spindle saw blade should not be greater than 0.05mm. Positioning can only be carried out after confirmation.