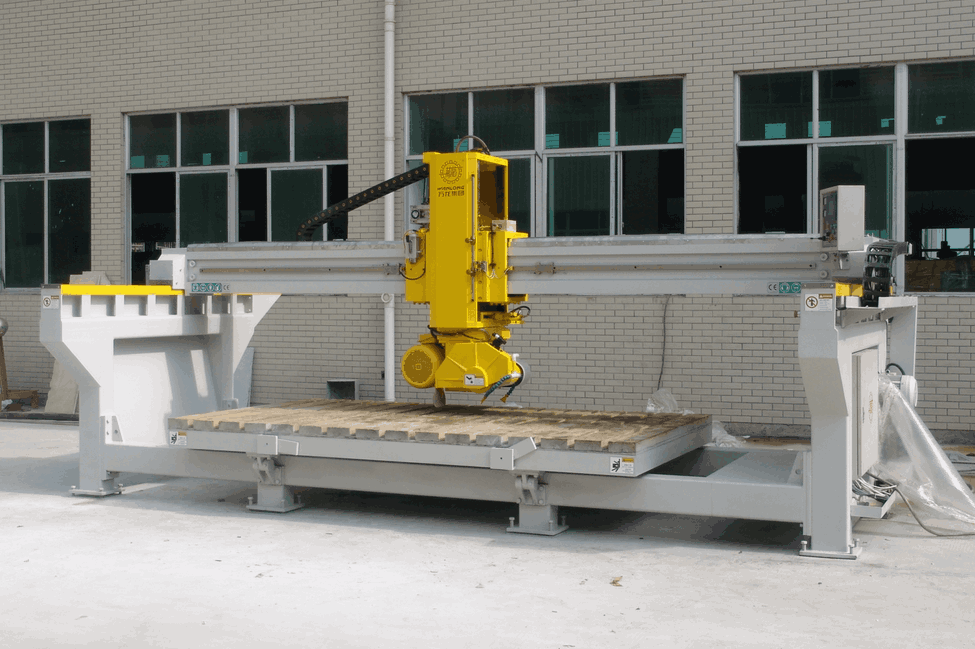
1. Do a good job of cleaning and cleaning the parts. The cleaning work includes the removal of residual foundry sand, rust, chips, etc. Especially some important parts, such as the gantry cutting machine, the inner cavity should be painted with anti-rust paint. Oil stains, rust or attached cuttings on the parts can be cleaned with diesel, kerosene or gasoline as a washing liquid, and then dried with compressed air.
2. Lubricant is usually added to the mating surface before mating or connecting.
Especially the bearing part in the spindle box component, the screw nut part of the lifting mechanism.
3. The matching dimensions of matching parts should be accurate, and the matching dimensions should be re-checked or spot-checked during assembly. For example: the matching part of the main shaft journal and the bearing, the matching hole of the main shaft box and the bearing and the center distance. 4. For wheel assembly, the axis of the two toothed wheels must be in the same plane and parallel to each other. Normal toothing clearance should be ensured, and the axial misalignment should be ≤2MM. 5. The joint surface of the joint should be checked for smoothness and deformation. Otherwise, it should be trimmed and burrs removed to ensure that the joint surface is in close contact, flat, and not skewed.
6. The seals should be pressed into the sealing groove in parallel, and they should not be twisted or deformed, and the sealing surface should be damaged or scratched. 7. The assembly requirement of the pulley is that the axes of the two pulleys must be parallel, and the center of the groove should be positive. If the deviation is too large, the tension of the pulley will be uneven, causing the belt to slip off and accelerate wear.
At the same time, the V-belt should be selected before assembling, and the length should be consistent to prevent vibration in the transmission. 8. The bearing should be cleaned before assembling and the anti-rust paint should be washed off before assembling; when cleaning, check whether the raceways and rolling elements are corroded and whether the rotation is flexible; when assembling the bearing, apply a layer of lubricating oil on the surface of the mating parts. If the pressure difference is too large, the assembly should be stopped for inspection; when assembling the bearing, the end without the model should be facing inward and against the shaft shoulder; the magnitude, direction, and position of the force should be appropriate when the bearing is set, and the raceway should not be this way. The rolling element should be struck evenly and symmetrically under the force, and no slamming is allowed. Ensure that the end face is perpendicular to the shaft to prevent the installation from tilting.
9. The threaded connection should adopt the anti-loosening device. The following commonly used anti-loosing devices should be selected according to the actual situation and design requirements; double nut anti-loosing; spring washer anti-loosing; split pin anti-loosing; stop washer anti-loosing round nut and flower cushion anti-loosing ; The tightening method of symmetrical multiple bolts should be tightened gradually in a symmetrical sequence, and the strip connectors should be tightened symmetrically from the middle to the two directions. The end of the bolted rib should protrude from the nut.
10. Perform inspection while assembling.
11. Do a good job of pre-driving inspection carefully. For example: check the completeness of the assembly work, the accuracy and reliability of each connecting part, the flexibility of moving parts, the normality of the lubrication system, etc.
12. Carefully monitor the startup process. After the machine is started, immediately observe whether the main working parameters and moving parts are moving normally. The main working parameters include the speed of the movement, the smoothness of the movement, the rotation of the main shaft, the lubricating oil pressure, the temperature, the vibration and the noise. Only when the various sports indicators are normal and stable at the start-up stage can the test run. 13. Carry out trial operation and test related items according to the acceptance conditions of various stone machinery products. For example: the adjustment and test of the cutting speed and stroke, the adjustment of the lifting motion stroke, the test of the spindle rotation accuracy, etc.