According to different specifications of different equipment and different uses, the length and matrix of the designed diamond segments are also different. So choose carefully when you use it.
Pay attention to the segment operation of the device. If there is abnormal noise, vibration, noise, etc. during cutting, it needs to be checked or replaced; the cutting segment that is not used temporarily should be placed carefully to avoid bumping.
Secondly, in daily use, there are also some points to pay attention to, such as understanding the changes of the equipment segment after being subjected to strong temperature, so as to handle it correctly.
Everyone is familiar with temperature. It cannot be seen or touched, but we can feel it all the time. It brings many benefits to our life, but also affects many things, such as plants, animals, and even it affects us, so the diamond segment of cutting equipment is no exception.
When using the cutting segment to process the stone, the cutting segment and the stone run at high speed with each other, generating a lot of heat energy. Due to the extremely poor thermal conductivity of the stone, most of the heat energy is directed into the mining area. The surface temperature of the equipment segment rises rapidly, resulting in graphitization of the segment and a decrease in cutting ability. The matrix of the diamond segment is hot exhausted, the rigidity of the strength root is reduced, the noise during stone processing is large, and the service life of the segment is reduced.
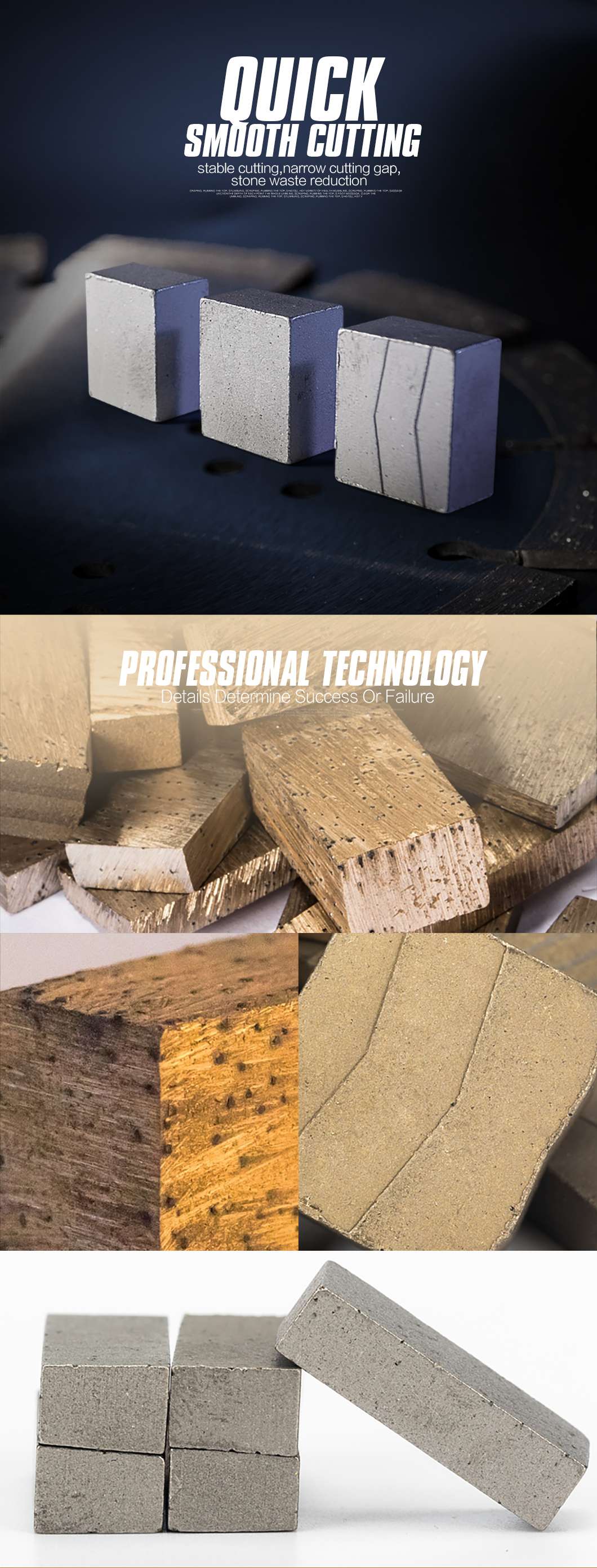
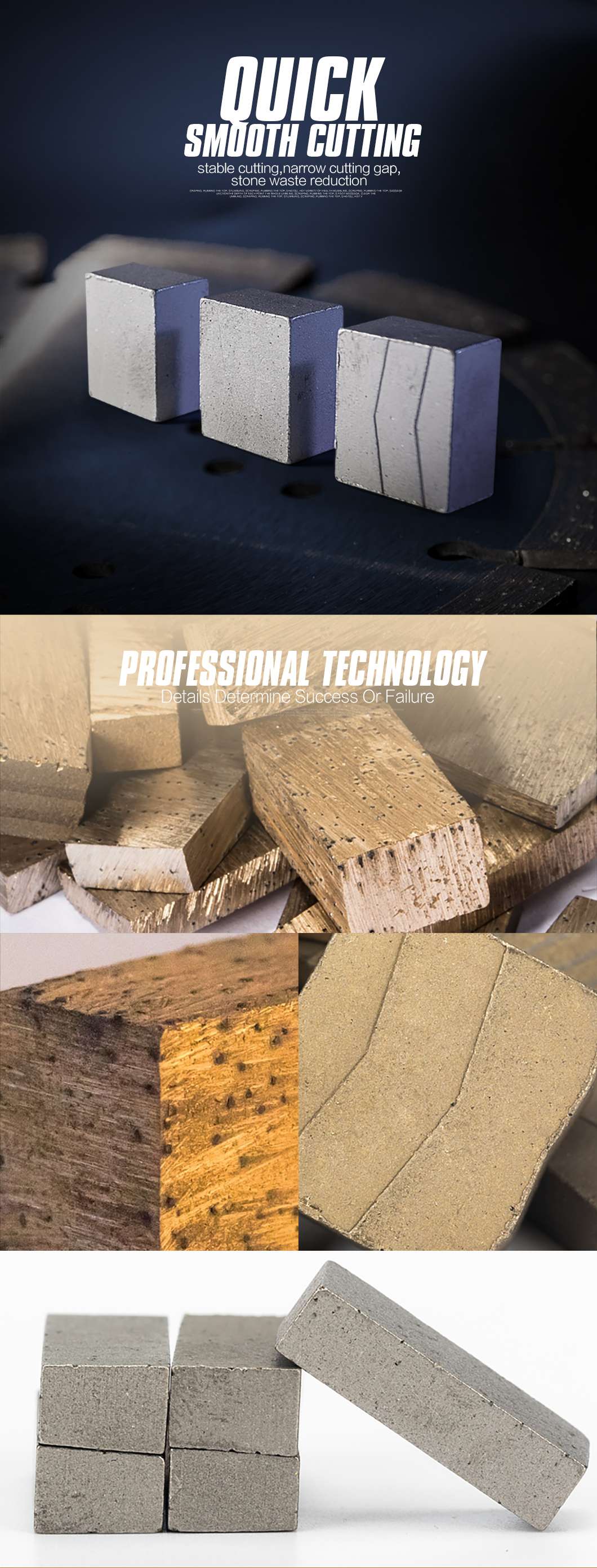
In addition to this, there is also the problem of wear on the side of the segment:
After the cutting segment is used for a period of time, the phenomenon of upper width and lower width appears, which is called side wear. So what is the reason for this phenomenon?
It may be due to poor quality, low strength, low edge layer concentration, low fine-grained diamond content, uneven matrix itself, mismatched metal matrix, and poor wear resistance.
Once a cut segment appears high in the middle and low on both sides or low in the middle and high on both sides, this degree of non-uniformity can result in segment wear.